提升产品质量是其中一个关键。
提升质量,我们需要做到:
提升产品的质量(提高合格率、提高客户服务水平)保证质量成本没有大幅度增加(或者不变甚至下降)在电子行业,SPC软件系统应用已成为标配。随着SPC在企业的作用越来越明显,越来越多的电子企业实施SPC应用。但在SPC领域,SPC软件良莠不齐,企业本身人员素质参差,导致很多企业SPC项目推进不断碰壁。
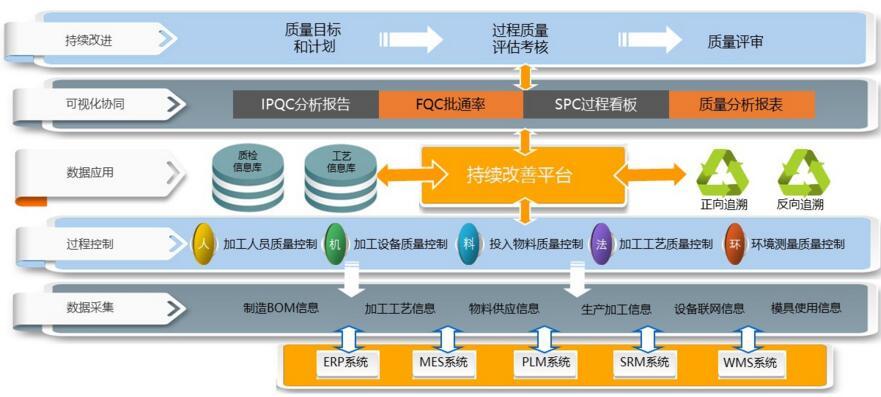
那么一个企业,SPC应用如何在企业快速落地?一个全新的SPC给出了答案。我们分享我们的一个客户案例
项目背景
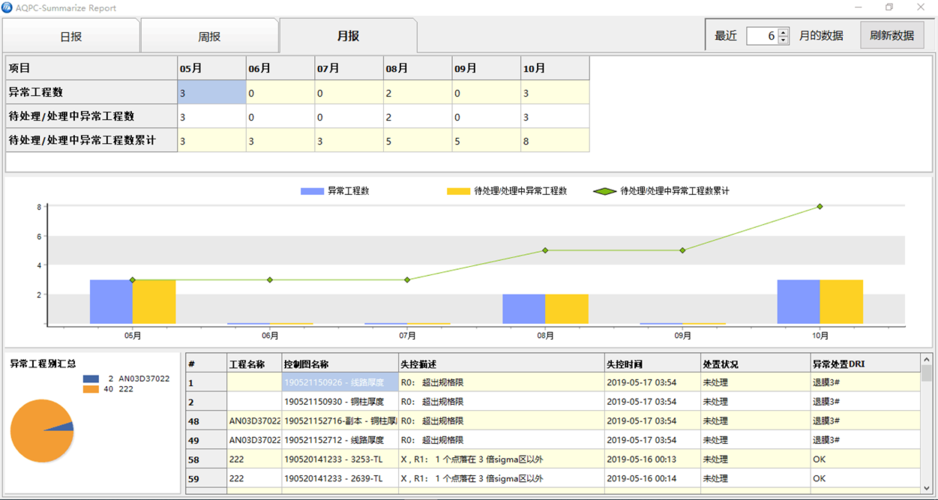
某家半导体封装工厂的质量管理与绝大多数封装测试工厂一样,有着行业同样的质量管理问题:
产品多样化,产能不断扩大;客户标准、质量报告、工序管控严格且复杂。从来料到封装测试,环节多而复杂。监控点数量大,SPC分析控制图成千上万,质量部工作量大。用excel或者minitab一个一个监控点做SPC分析控制图。很多监控点每天每小时更新,手工做SPC控制图赶不上数据的产生。负责SPC控制图的质量员工都不想干了。问题发现不及时将造成不小的成本损失。一、识别关键特性
为了在SPC项目中取得成功,首先需要识别和定义关键的质量特性。这些特性是产品和生产过程中最重要的参数,直接影响产品的最终质量。识别关键特性有助于企业集中资源和努力进行监控和改进。
二、定义监控过程
2.1 定义判异规则
设定明确的判异规则,以便在生产过程中及时识别异常情况。
2.2 配置检测项目
根据识别出的关键特性,配置相应的检测项目。
2.3 配置数据采集和进行数据采集
配置自动化的数据采集系统,确保数据的实时性和准确性。
三、实时监控和反馈
3.1 邮件监控
通过邮件系统实时监控生产数据,及时发现异常。
3.2 监控接口
推送到企业微信等第三方平台,实现实时通知。推送到QMS(质量管理系统)创建质量改善流程。四、监控可视化
在车间合适的位置放置合适的SPC监控看板,每个看板都可以显示不同检测点的SPC实时监控数据。这种可视化方式有助于生产管理人员及时了解生产状态,并迅速采取相应措施。
五、分析和报告
对历史数据进行分析,找出长期趋势和潜在问题。详细的SPC分析报告包括控制图、正态性检验、彩虹图、子组分布图、分布拟合、能力分析直方图、机器学习判异图、能力对比图、数据摘要等多种分析工具,为质量改进提供全面支持。六、成果
在严格遵循上述步骤,将SPC项目落地后,公司在一年内实现了如下成果:
机器和生产流程稳定:实时判断制程偏移趋势;发现问题后,第一时间处理;从根本上解决问题,减少问题重复发生;良品率提高:通过持续改进减少生产过程中的缺陷产品;客户满意度提高:实时SPC系统保证了产品的高品质,公司会以季度为单位,定期对生产过程状态评估,制订相应改进计划,确保SPC实施的有效性。效益明显:虽然实施SPC有适量的投入,但质量人员工作量下降了,设备稳定性提高了,直接间接提高了人员工作效率。合格率提高了,报废率下降了,成本降低了。这就是我们其中一个客户的实施的SPC项目过程,不管你用什么SPC产品,对你们计划实施SPC相信都有一些帮助。