• 2,促进对所需更改的早期识别;
• 3,避免晚期更改;
• 4,以最优的成本及时提供优质产品。
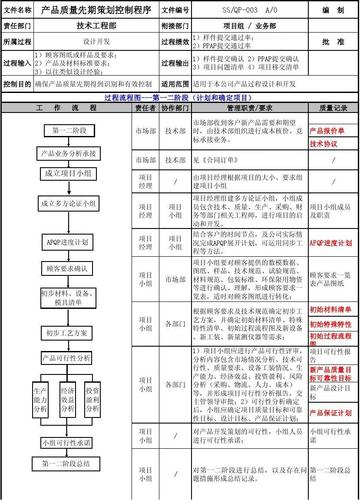
• 1,)组建APQP小组,小组由多方参与,指定APQP小组过程负责人。
• 顾客参与、供应商参与,以及小组内相关部门指定人员,建立横向职能小组。
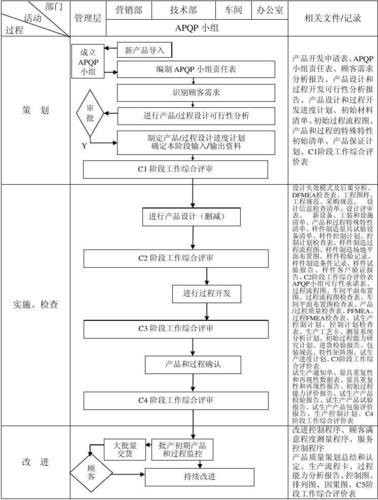
2,)确定范围:在产品项目的最早期,重要的是识别顾客需要、期望和要求。
• 对所提出来的设计、性能要求和制造过程评定其可行性。
• 确定成本、进度和必须考虑的限制条件。
• 确定所需顾客的协助
确定文件化过程和方法。
三、实施要点• 沟通:确定定期会议
• 培训:顾客要求和期望,开发所需技能等。
• 控制计划:不同阶段的控制计划的作成, 要有样件阶段、试生产阶段、生产阶段的控制计划。
• 建立规定职责和时间进度的矩阵表,来跟踪解决问题。
• 产品质量的进度计划:考虑产品的类型、复杂性和顾客的期望。进度图应列出任务、和/或其他事项,跟踪进展和制定会议日程的统一格式。每一事项必须具备“开始”和“完成”日期,以及实际完成日期。标识特别注意项目,监控项目进度。
• 确保符合或提前于客户的进度计划。
四、各阶段输入及输出阶段一:计划和确定项目
输入:
• 顾客的声音:市场研究、保修记录和质量信息、小组经验
(来自内外部顾客的抱怨、建议、资料和信息)
• 业务计划/营销策略
• 产品/过程标杆数据
• 产品/过程设想
• 产品可靠性研究
• 顾客输入
输出:
• 设计目标(目标要可测量的,包括适用的法规要求)
• 可靠性和质量目标
• 初始材料清单(包括潜在供应商名单)
• 初始过程流程图
• 产品和过程特殊特性的初始清单
• 产品保证计划(质量计划的重要组成部分)
• 管理者支持
阶段二 产品设计和开发
输入:上个阶段的输出
设计部门输出:
• 设计失效模式及后果分析(DFMEA)
• 可制造性和装配设计
• 设计验证
• 设计评审
• 样件制造(含控制计划)
• 工程图样(包括数学数据)
• 工程规范、材料规范
• 图样和规范的更改
APQP小组的输出:
• 新设备、工装和设施要求
• 产品和过程特殊特性
• 样件控制计划
• 量具、试验设备要求
• 小组可行性承诺和管理者支持
阶段二 产品设计和开发设计评审应包含以下内容:
• 设计/功能要求的考虑;
• 正式的可靠性和置信度目标;
• 部件/子系统/系统工作循环;
• 计算机模拟和台架试验结果;
• 设计失效模式及后果分析(DFMEA);
• 可制造性和装配设计的评审;
• 试验设计(DOE)和装配产生的变差结果;
• 试验失效;
• 设计验证进展,使用设计验证设计和报告(DVP&R)来跟踪设计验证进展。
阶段三 过程设计和开发输出:
• 包装标准
• 产品/过程质量体系评审
• 过程流程图
• 车间平面布局图
• 特性矩阵图
• 过程失效模式及后果分析(PFMEA)
• 试生产控制计划
• 过程指导书
• 测量系统分析计划
• 初始过程能力研究计划
• 包装规范
• 管理者支持
阶段四 产品和过程确认输出:
• 试生产(采用正式工装、设备、模具,最小数量由客户设定,产品可用于做SPC/MSA/A过程评审、生产确认试验等)
• 测量系统评价
• 初始过程能力研究
• 生产件批准
• 生产确认试验
• 包装评价(正常运输中和不利环境下受到保护)
• 生产控制计划
• 质量策划认定和管理者支持(对控制计划、过程指导书、量具和试验设备进行评审)
阶段五 反馈、评定和纠正输出:
• 减少变差(使用控制图或其他统计手段识别变差,减少普通原因引起的变差,注意特殊原因引起的变差。)
• 顾客满意
• 交付和服务
控制计划:是质量策划过程的重要体现,描述了过程的每阶段所需的控制措施,包括保证所有的过程输出将处于控制状态的进货/过程中、出厂和阶段性的要求。在正式生产中,提供了用来控制特性的过程监视和控制方法。在整个产品寿命中被保持和使用。